Sutton Courtenay Environmental Education Centre

After many years of work for Bucks. Berks. Oxon. Wildlife Trust on various small projects, we were invited to design for them a new-build field study centre on land owned by Didcot Power Station. A negotiated contract for the building work was used with Neil May Builders. The building was completed in 2002.
The field study centre at Sutton Courtenay is used by around 10,000 local schoolchildren each year, as well as community groups and adult learners. The design brief was to build a centre that would inspire and educate generations of youngsters about their impact on the natural environment. The building has been built to be near carbon neutral in its space heating and hot water requirements, with electricity use vastly reduced by high daylighting levels. Overall the building was designed for significantly reduced CO2 emissions compared to having designed it to the (then current) 2002 regulatory standards. Ongoing monitoring of the centre’s energy and water consumption will continually assess whether these dramatic targets are being genuinely achieved – in the short, medium and, hopefully, long-term. (see monitoring section)
The building is an enlightening educational resource that inspires us to take positive action for the environment.
– Mike Moreton, SCEEC
The building design incorporates the following:
- Structural rammed earth blockwork & lightweight interlocking clay block partitions
- Waterless urinals & low water usage sanitaryware
- Rainwater collected & used for flushing toilets and general cleaning uses
- On-site “separation and compost” sewage treatment system
- Clean burning wood stoves for space and hot water heating
- Natural clay plasters
- Ecological self levelling and self colouring floor finishes
- Natural paints and finishes throughout
- Home-grown cedar shingles for upper rooves to collect rainwater
- Passive solar design as key to building’s orientation and position
- Super-insulated British made timber ‘I’ beam structural frame
- Sheep’s wool and recycled cellulose fibre insulation materials
- Turf roof to the lower rooves of the building to replace lost habitat area
- P.V/Thermal hybrid Solar panel to provide summer hot water in addition to stove
- To see details of events at the centre or arrange a visit: www.bbowt.org.uk/pages/education/sutton.htm
Architectural Introduction; the site
Through a strip of dark woodland, with its ruined remnants of ordnance buildings and a variety of mature trees lies a meadow, full of teasels, opening out to the south and east, basking in morning and midday sun. This meadow extends over several acres towards the Didcot A and B power stations to the east and is bounded to the north by an old path that runs parallel to a dense hedge. To the south a group of large willows provides a buffer between the meadow and a concrete block factory.
While exploring the site and understanding the larger defining characteristics of the site, many things begin to act as anchors for organising and orienting the building: a particular view of a poplar we wanted to ‘frame’ with one of the openings in the building; the hedge providing a great opportunity to provide bird watching windows to the north; and a wildlife garden in the space between building and hedge.
Our response
We saw the unique juxtaposition of natural and manmade landscapes and boundaries present on this site as a great opportunity to further develop our office’s expression of an architecture that responds to both historical and natural elements, and to broader ideas of social and environmental ‘sustainability’.
The design aimed to resonate with our experiences of exploring the reserve, particularly elaborating on the border condition of the northwest corner of the meadow, where the hedge met the woodland.
The need for the Centre to be accessed from the road, and our reluctance to take vehicles too far onto the reserve indicated a site close to the road, but beyond the narrow strip of woodland immediately adjacent and into the meadow beyond – to maximise day lighting and solar gain. Discussions with the clients on how the woodland and meadow would be managed, and how children currently used the reserve helped us choose the final position of the centre and it was agreed to site the centre in the northwest corner.
Client response to design process
An initial design was enthusiastically received by the Trust, but after cost related re-design, a subsequent proposal was received with less enthusiasm. As we knew that so much of the quality of the building was to lie in subtle effects of lighting, of its relationships to the different natural boundaries of the reserve and the use of natural materials, an artist’s impression was used to express to the client the mood and tone of the building. This was successful in convincing the client that the simpler building retained the initial qualities that the Trust found attractive.
BUILDING PERFORMANCE
The building’s staff worked with Peter Warm, energy consultant on energy monitoring for the first two years’ use.
AECB’S CLP PROGRAMME; CURRENT ASSESSMENT
Utlility bills (water and electricity) for the centre and the amount of cordwood burnt for space heating is being continuously recorded. This data will be entered into the low energy buildings database being developed by the AECB’s CarbonLite programme (www.carbonlite.org.uk). Meanwhile the first two years monitoring of the energy and water consumption of the centre has been uploaded here.
MONITORING FIRST TWO YEARS
Peter Warm (Environment Conscious Building Services) worked with the building’s staff to monitor the energy and water used in the building. The results show that the original design claims – to produce a building that would reduce its CO2 emissions by 90% for space and water heating – were achieved in reality. The figures also show that the CO2 emissions put out by operating this building, including all internal and external lighting, office and kitchen equipment and appliances, were 3.3 tonnes of CO2 per year (12.75kg of CO2 per square metre and year).
JUSTIFYING CLAIMS; LEARNING FROM MISTAKES
The monitoring of water and electricity consumption is based on meter readings, but no sub-meters were installed to differentiate between, for example, electricity consumption for lighting vs. office equipment – due to lack of available funding for this purpose, but we have learnt a few important lessons:
* Using local wood as a fuel source allowed us to create a building emitting very low amounts of CO2, at the expense of some degree of particulate air pollution. Wood fuel used at individual building level is not a panacea, however may remain part of the sustainable fuel mix for rural / off grid / educational / demonstration type buildings.
Note added Dec 2007: There is growing evidence that both producing woodfuel and burning it can lead to higher levels of greenhouse gases (other than CO2) being emitted than previously thought. This is an area that requires some serious consideration given the popular support for wood as a ‘low carbon’ or ‘low greenhouse gas’ fuel.
* Using such a low carbon fuel source (but see comment above!) allowed us some freedom in design: a building with a high wall/roof to floor ratio – i.e. it ‘sprawls’, i.e. not a compact building form – we would say ‘expressive’, ‘exploring the site’. We therefore traded away some energy conservation that would have benefitted from a more compact form (i.e. ‘spent’ some of our CO2 ‘allowance’) by being freer or more expressive with the building shape.
* Again, because of using wood, we have not ‘felt’ the effects of thermal bridging and air leakage – increasing the building’s heat loss – in the running costs or significantly in the CO2 emissions. If a building like this were run on gas, we would ‘see’ more accurately the effects of such thermal defects showing up in the fuel bills. The complications, uncertainties and innaccuracies of trying to accurately monitor the calorfic value of cordwood burnt for space and water heating has not allowed us to fully understand the actual thermal performance of the building’s envelope. Thermal imaging of the building combined with a thorough study of our detailed construction drawings related to the apparent defective areas would no doubt indicate how we could become more effective at designing out thermal bridging, and increasing airtightness of the building fabric.
We are in no doubt of course that construction junctions in certain areas of the building are thermally imperfect – either/both through design or workmanship! The effects of these thermal defects can possibly be ‘felt’ in cold weather on a Monday morning (followng no weekend use / heating), when we expected room temperatures to have held more constant than is in fact the case. Higher than hoped for air leakage through construction joints is most likely to account for the more significant heat loss mechanism, with excessive thermal bridging at building junctions being less significant in this building.
* In addition to the factors above, the use of a more automated heating system (likely with gas as a fuel) would inevitably result in most building’s users ‘cranking’ up the temperature and increasing their CO2 emissions, in line with their internal temperatures. Burning wood in wood stoves keeps a direct, manual link to the occupants’ building related CO2 emissions associated with space heating. The Centre can be heated with wood to reach perfectly acceptable comfort conditions with very low CO2 emissions: ‘overheating’ the building in the heating season becomes harder work, and acts to some degree as a self limiting system, similar to a gentle form of fuel rationing. It is also cheap to run.
* Lighting related electricity use is likely to be very low, the bulk being accounted for by office equipment and appliances.
* LESSONS LEARNT are therefore:
- BETTER DETAILING TO REDUCE AIR INFILTRATION
- BETTER DETAILING TO REDUCE THERMAL BRIDGING
- BETTER WORKMANSHIP AND SUPERVISION PRACTICES RELATING TO THE ABOVE
- TRY AND AFFORD SUB METERS
- TRY TO AFFORD A MORE SOPHISTICATED MONITORING PROGRAMME.
SUMMARY OF ONE YEAR’S FUEL USE
Electricity** 5,607.62 kWh/yr = 2,299.12 kgCo2
Passive and active solar*** 1,764.17 kWh/yr = 0.00 kgCo2
CO2 COEFFICIENTS APPLIED, UNITS kgCo2/kWh
* WOOD 0.03
** ELECTRICITY 0.41
*** SOLAR 0.00
Total Tonnes Co2/annum: 3.3
Staff counted the number of boxes of firewood burnt each month in the centre’s two wood stoves. Electricity and water consumption data were taken from utility bills for that period.
BASIC INFORMATION SUMMARY
Monitoring period: April 03 – Sep 05.
Fuel types: Wood (logs / waste timber)/ Solar / Electricity (grid)
Floor area
Net floor area (internal floor space not whole building footprint) = 234m2 + 25 m2 mezzanine.
Total: 259 m2 net floor area.
All our portfolio projects
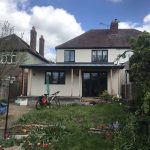
Shropshire retrofit / extension
The project brief asked for dramatic increase of energy efficiency for this 1950’s semi-detached house, with a single storey extension to the living space facing the back garden. The budget was modest so it was clear that the AECB’s Level 2 Retrofit Standard would be a good target. https://aecb.net/aecb-carbonlite-retrofit-standards-level-1-and-2/ Our clients were a pair of novice self-builders, already armed with a good amount of research into the subject, allowing them...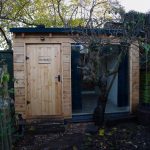
Summerhouse
A garden outbuilding in Hereford, designed by Andy Simmonds, built by Fraser Williams with apprentice, Raimi Wye. Complete Summer 2022. Brief description from Fraser ‘ We built this garden room in the summer of 2022. I was the main carpenter working alongside apprentice Raimi Wye. Andy Simmonds provided a lot of practical support during the build – such as input on building details and construction techniques – and drew up all...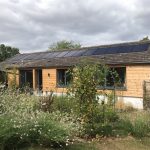
Ridge
Retrofit of 1960’s bungalow in the Malvern area. Completed towards the end of Summer 2022. Design to AECB Retrofit Standard – see https://aecb.net/aecb-retrofit-standard/ Project management and specialist contractor – www.ecovertsolutions.co.uk Main Contractor Oneport Building Ltd. This was the second retrofit scheme that we’ve worked on a ‘better building model’ – lockdown meant progress on some of these jobs was very slow – good builders even harder to come by than...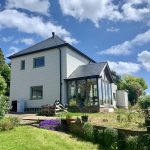
Chestnuts
The Chestnuts featured in a ‘Passive House Accelerator’ webinar in May ’22 See links to Youtube recordings here : Partel: https://www.youtube.com/watch?v=lCaZO6ufW94 Accelerator: https://www.youtube.com/watch?v=YEsFV-pVsjg&list=PLnIli3Bt55ttDSGau60bjJfL72NgJ3uD7&index=7 It also features on pg. 98 of their Summer magazine. See this link https://indd.adobe.com/view/f47041e2-3d1b-4a33-a706-ea6e582ba7e3 This is a near-Enerphit standard retrofit of a 1950’s detached house in Chepstow. After months of waiting through the lockdowns of 2020, a contractor from Newport was selected to work alongside https://www.ecovertsolutions.co.uk/ The...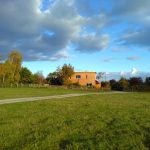
Honeycroft
Our clients here had a small cottage with extremely narrow stairs to a limited head height loft area. It quickly became clear that a replacement dwelling was the best option. We designed a timber frame flat roof house; this has achieved Passivhaus target for energy efficiency. The completed project is not yet certified, but that is the clients’ intention. The house was built by local passivhaus / timber frame specialists,...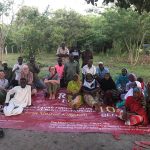
Tanzanian Eco-Village
2023 update: A building test unit was built in 2018 and 12 months of data showed what worked and what needed to be improved for the new 10-person house An experimental sewage system was built in 2020 The new 10-person house (House 5) was completed this year – we have 3 months T & RH data House 5 improved experimental sewage system built. A selection of photos from March 2023...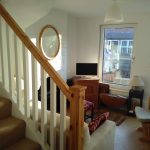
Hereford retrofit
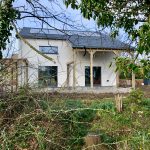
Llanforda
A new replacement dwelling in Oswestry was complete in January 2020. A draughty 1970’s bungalow with subsidence issues on the site would have been expensive and difficult to improve to near Passivhaus standards of energy efficiency. After debate on pros and cons, it was decided to demolish the bungalow and build a near-Passivhaus two storey dwelling. This choice gave the chance to place the house to allow increased solar access...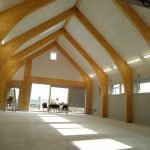
Garway Community Centre
The rural Herefordshire village of Garway finally has its new Passivhaus certified community centre. It has taken many years’ development, but a successful bid to Big Lottery Fund in 2016 made the project a reality.The building was completed with a grand opening in April 2018. The centre provides many functions for the village, including a large multi-functional hall with full stage / green room etc; an outreach medical centre; a cafe/bar, part-time...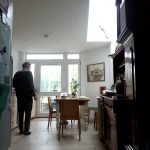